This is a repost of the original paper available on Odysee: https://odysee.com/@hoffmantactical:3/Mechanical-Test-Results-of-Filled-PA-and-PET-3D-Printing-Filaments
Summary
Eight Polyamide and three Polyester filaments were tested with the goal of comparing the mechanical performance of these two groups of materials. Testing was done in sets beginning with tensile testing, creep testing, impact testing, and ending with layer adhesion testing. Poor performing filaments from earlier tests were eliminated in later testing.
Polymaker PLA Pro was included in most of the tests as a reference point to compare the other filaments to.
The results show that Polyester based filaments can be a good alternative to Polyamides, solving the poor stiffness and creep issues of the latter. However, some of the Polyamides performed better than others and may be better than the Polyesters in terms of durability.
Testing Method
All testing was done at 75 to 85 F. The results at significantly higher or lower temperatures would no doubt be different.
Real world conditions were simulated for all samples by exposing them to a saturated environment prior to testing to allow them to absorb water. The Polyamide samples were all annealed at ~185 F prior to water exposure as this process greatly improves the mechanical properties, particularly in regard to creep. The Polyester filaments were not annealed because it was not believed that annealing would provide significant benefits.
Tensile and creep samples were printed horizontally with sufficient walls to ensure that only the absolute material strength was tested. Print settings were adjusted for maximum line to line adhesion to prevent line separation during necking.
The same print settings are used for impact samples except that aligned rectilinear infill was used to produce a part with all print lines running perpendicular to the fracture zone.
Layer adhesion samples were printed vertically with an additional cooling tower that allowed the layer time to be near that of a realistic part. Settings were adjusted for optimal layer adhesion, and care was taken to ensure that all samples were printed in the same environment.
The tensile testing apparatus used does not have a strain gauge. The distance that the sample is pulled is recorded instead. This adds significant error to the stiffness data as the machine’s flexibility is added to that of the sample. A scaling factor of four was used to bring the results closer to reality, but this is only a patch. The results may still be used comparatively to mark some filaments as stiffer than others.
Creep testing was conducted by supporting a fixed weight from the creep samples. This applied a constant stress which allowed the sample to strain over time. Each creep test was conducted for three days. The length of the neck portion of the sample was measured before and after testing to capture the strain.
Impact testing was conducted using a unique vertical impact testing apparatus. A guillotine style hammer falls along guide rails and strikes the end of the rigidly mounted sample. The speed of the hammer is recorded with and without a sample to calculate the amount of energy absorbed by the fracture.
Three samples of each material were tensile and impact tested. Only two samples were used for each creep test due to limited space. The average across samples is used as the final result unless one of the samples had a drastically different value.
Tensile Results
The following Polyamide filaments were tested for absolute material strength:
- Atomic Filaments Nuclear Nylon (NN)
- Bambu PAHT-CF (PAHT-CF)
- COEX Nylex Glass Fiber (COEX)
- Markforged Onyx (Onyx)
- Polymaker PA612-CF (PA612-CF)
- Polymaker PA6-CF (PA6-CF)
- Polymaker PA6-GF (PA6-GF)
- Polymaker PA12-CF (PA12-CF)
The following Polyester filaments were tested for absolute material strength:
- Bambu PET-CF (BB PET-CF)
- BASF PET-CF15 (BF PET-CF)
- Polymaker PET-CF (PM PET-CF)
Note that filaments are listed here by brand and then the name assigned by the brand. The short name for the filaments in italic will be used from now onwards.
COEX and PA6-GF were the only glass fiber filled materials. The rest of the filaments are carbon fiber filled.
Young’s Modulus is a measurement of stiffness. It is calculated from the slope of the stress vs. strain curve. The stiffness data for all twelve filaments is shown in Fig. 1.
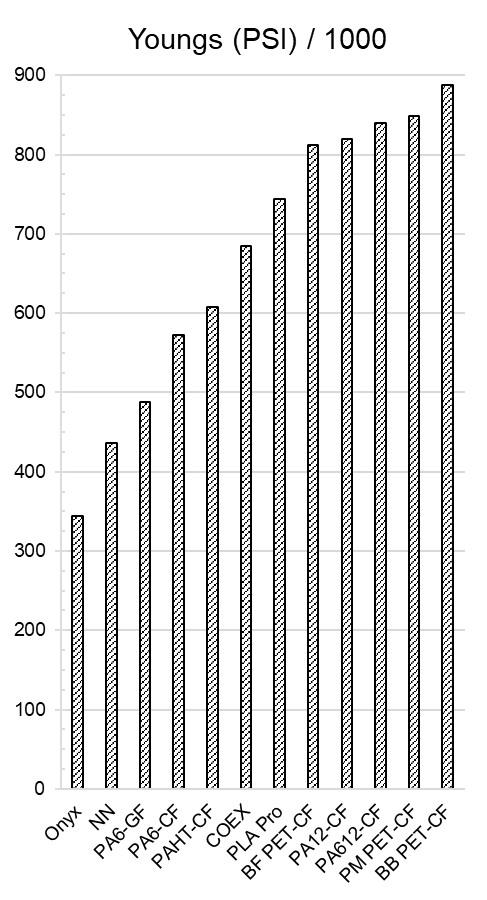
The PLA Pro is a proven filament for many parts that are replaced by the Polyamides or Polyesters only due to their higher temperature resistance. It marks a good stiffness value.
Most of the Polyamides are less stiff then the PLA Pro, making them poor choices for rigid parts.
The PA-CF is significantly stiffer then the PA-GF, indicating the stiffer properties of carbon over glass.
The BB PET-CF is significantly stiffer than the BF PET-CF, probably due to a higher carbon content.
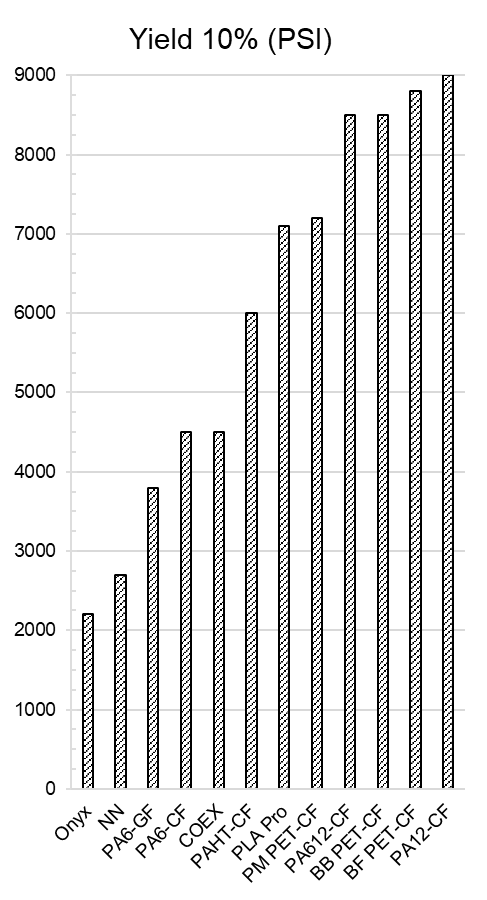
Yield strength is the point at which permanent plastic deformation begins. It is found by inspecting the Young’s Modulus vs. the stress. As the material begins to yield, the stiffness is reduced. A 10% loss of stiffness was chosen as the threshold for these yield strengths. A lower threshold would yield different results, probably favoring the Polyamides somewhat more. The yield strength for all twelve filaments is shown in Fig. 2.
Yield strength is an important metric as it is analogous to the maximum working load of the material. The same five filaments that were stiffer than PLA Pro also have a higher yield point then PLA Pro.
The PM PET-CF has fallen behind significantly from the other Polyesters, while the BF PET-CF has moved up. This interesting observation displays that a greater elasticity does not mean lower strength.
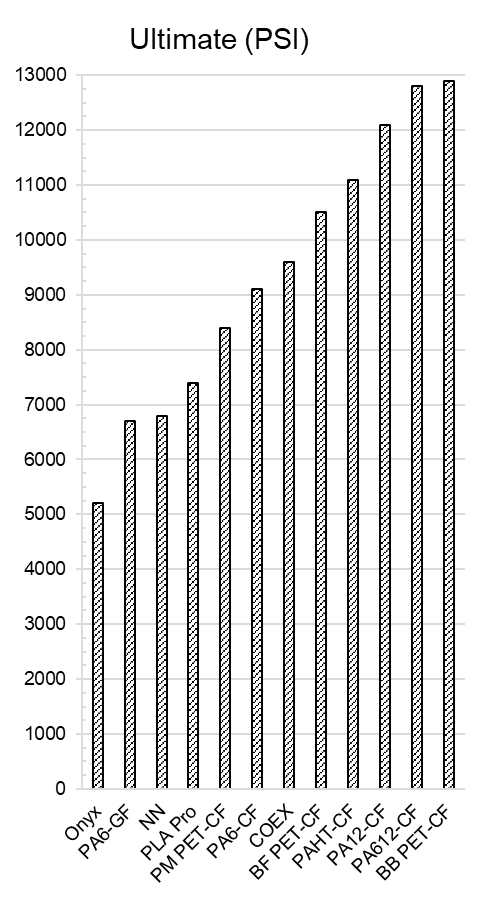
Ultimate strength is the amount of stress required to cause catastrophic fracture or necking. It is the maximum stress measured during testing. Fig. 3 displays the ultimate strength of all twelve filaments.
The ultimate failure point of a material is the least important in determining if it will sustain a particular load within specified strain limits.
The same trend from the yield strength results is generally true. The PLA Pro and PM PET-CF have fallen behind, while the PAHT-CF has pulled ahead.
The higher ultimate strengths of the Polyamides are due to their high ductility. A quality that, standing alone, has not been found to be useful.
The lower relative ultimate strengths of the PLA Pro and PM PET-CF are due to these materials having very little ductility prior to failure. This can be seen by how close the ultimate and yield strengths are. The significance of this is not known.
Agreement between the triplets of samples was within 8%.
Creep Results
Creep testing has one significant challenge. The amount of absorbed water in the sample has a significant effect on the size of the sample. The addition of water causes expansion and the reduction causes contraction. To help combat this issue, samples were measured before and after water exposure. During testing, samples continued to be exposed to a saturated environment. After testing, samples were measured, dried, and remeasured. This gives some assurance that the results are not driven by moisture and do in fact indicate the strain due to creep. Despite these precautions, some obscurity still remains.
All creep samples were loaded at 2000 PSI for 72 hours. This is significantly below the yield point of the materials tested and all deformation found can be attributed to creep.
Only five of the twelve filaments were tested for creep. These were chosen based on their merits in the tensile testing or because they make a good representation of their general type. Testing all of the filaments was not practical due to the time and space required to conduct such testing.
The following four Polyamide filaments were creep tested:
- COEX Nylex Glass Fiber (COEX)
- Polymaker PA612-CF (PA612-CF)
- Polymaker PA6-CF (PA6-CF)
- Polymaker PA12-CF (PA12-CF)
The following Polyester filament was tested:
- BASF PET-CF15 (BF PET-CF)
PLA Pro was not tested. However, it is not known to have any significant levels of creep and is most likely similar to the polyester.
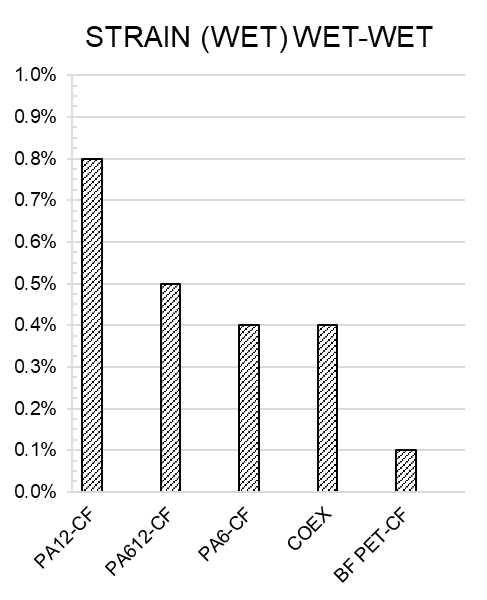
Fig. 4 illustrates the strain calculated from the two wet measurements immediately before and after the creep testing process.
PA12-CF suffered the worst creep, a fact which has been confirmed by observing creep on parts in the field. BF PET-CF suffered almost no creep, which is one of the attractive points of the Polyesters. The higher level of creep suffered by the PA-6 and COEX may be an issue in some cases. Creep has not been a large issue with these filaments during use in the field.
Before considering the position of the PA612-CF we must inspect Fig. 5 produced from the dry measurements taken prior to water exposure and those taken after drying the tested samples.
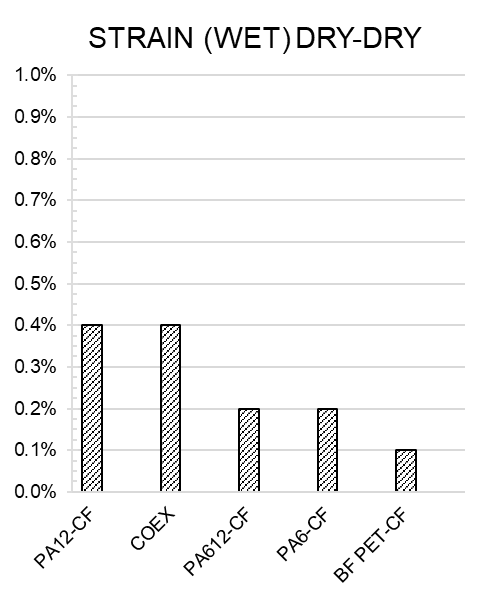
Most of the Polyamides have a lower overall strain than was seen in Fig. 4. This is probably due to the samples absorbing additional water during the strain test, resulting in expansion in addition to the creep. The water leaving the sample during the drying process reversed the expansion leaving only the creep behind.
This discrepancy is due to a flawed testing method. These results should be considered with this in mind.
While specific values may not be correct, some general trends can be observed. BF PET-CF had very low creep, PA12-CF has higher creep, and PA612-CF has similar creep to the other Polyamides.
It is important to point out that this testing was done in a saturated environment. The PA612 and PA12 were tested prior to this in a dry environment with less than 0.1% strain measured in both cases. It appears that Polyamides creep more when wet.
Agreement between the pairs of samples was within 0.1%.
Impact Results
Only six of the twelve filaments were tested for impact resistance. These were chosen based on their merits in the tensile and creep testing or because they made a good representation of their general type.
The following two Polyamide filaments were impact tested:
- Polymaker PA612-CF (PA612-CF)
- Polymaker PA6-CF (PA6-CF)
The following Polyester filament was tested:
- BASF PET-CF15 (BF PET-CF)
- Bambu PET-CF (BB PET-CF)
- Polymaker PET-CF (PM PET-CF)
Fig. 6 illustrates the results of impact testing. Units are thousandths of a Foot Pound absorbed by the breaking sample.
Only one of the PA6-CF samples broke, absorbing 1270 mFTLB. The other two samples simply yielded a small amount and stopped the hammer. The hammer carries approximately 1.6 Foot Pounds of energy at six Feet per Second. The failure to break indicates that the samples had greater than 1600 mFTLB of resistance. 1500 mFTLB has been used as a placeholder value for the sake of comparison.
One of the PLA Pro samples broke, absorbing 1400 mFTLB. This data was discarded as an outlier. Such sporadic impact results have been observed with PCTG as well as PLA. The mechanism of this is unknown.
The PLA Pro and PA612-CF had similar resistance to impact. This makes the PA612 a well rounded filament with a good balance between strength and impact resistance.
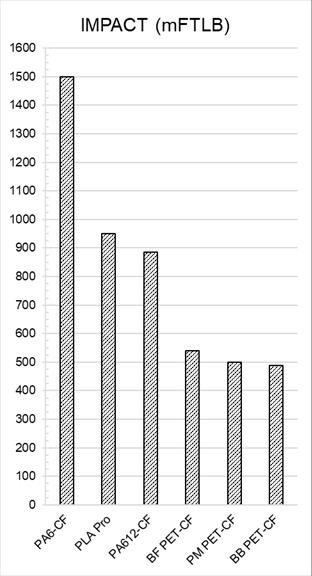
All of the PET-CF filaments had significantly lower impact resistance. They are still higher than many PLA and PETG filaments, which can have values below 200 mFTLB.
The very high resistance of the PA6-CF makes it a good option when great toughness is needed. Interestingly, the PA6-CF also has significant ductility, indicating that with Polyamides, higher ductility can produce greater impact resistance. The same has not been true for other filaments such as PETG.
An important note is that this testing was done on wet samples. Earlier testing done with a glass filled Nylon has shown a significant loss in impact resistance as the sample dries out. This loss is accompanied by a gain in stiffness and strength.
Other than the above notes on the PLA Pro and PA6-CF, agreement between the triplets of samples was within 10%.
Adhesion Results
Layer adhesion testing was only conducted on five of the twelve filaments. The following three Polyester filaments were tested:
- BASF PET-CF15 (BF PET-CF)
- Bambu PET-CF (BB PET-CF)
- Polymaker PET-CF (PM PET-CF)
The following Polyamide filament was tested:
- Polymaker PA612-CF (PA612-CF)
Fig. 7 illustrates the layer adhesion results. Values represent the ultimate tensile strength, which is the point where all samples broke completely with little or no yield. The PA612-CF was the only filament to demonstrate a measurable amount of yield prior to breaking.
PLA Pro had the best layer adhesion at just over 5 KPSI. This is due to the ambient printing temperature being close to the melt temp. The other filaments performed substantially worse, but would most likely perform closer to the PLA Pro if a heated enclosure had been used.
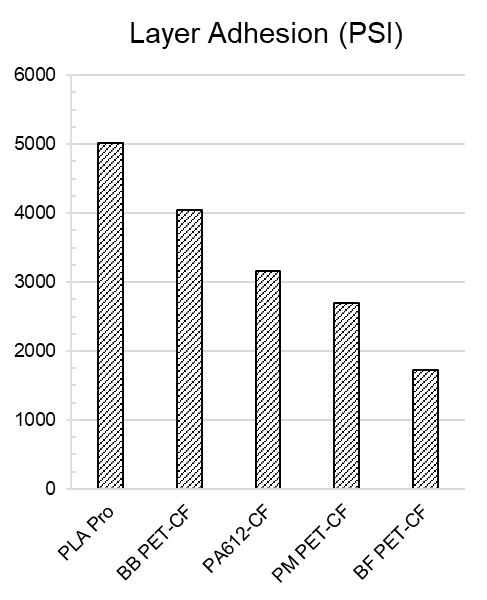
The BB PET-CF performed very well at just over 4 KPSI. Surprisingly, the BASF had poor layer adhesion well below 2 KPSI, ruling it out as a competitive option among the Polyesters. The PM PET-CF and PA612-CF were better than the BF PET-CF, but still below the BB PET-CF.
The BF PET-CF was tested several times to verify its poor performance. Results were consistent.
In general, layer adhesion testing has lower consistency then the other tests. Agreement between triplets of samples was within 15%, except in the case of the BB PET-CF, in which one sample tested almost 25% less than the others. Because of this, and the many variables that affect layer adhesion such as the ambient temperature, the results should be used with care.
Conclusions
When deciding what filament is best for a particular application, care must be taken to consider the mechanical requirements of the part in question. The discussion here will be conducted with the focus of deciding what filament is best for manufacturing rigid parts such as firearm receivers and accessories. For parts with flexures, bumpers, or those subject to great impact forces, the optimal filaments will most likely be different.
PLA Pro is a filament many mechanical parts have been made from with good results. It has sufficient strength and stiffness to function in this role. While filaments weaker or less stiff than PLA Pro may work for a particular application, they are considered inadequate here because of the unproven nature of their lower strengths.
Most of the Polyamides were less stiff than the PLA Pro and will be marked as inadequate.
COEX and PA6-CF have both been used in real world applications with only minor creep issues once annealed. The similar levels of creep experienced by the PA612-CF indicate that it will also be practical in real world applications. The significantly higher creep of the PA12-CF marks it as inadequate.
All three of the Polyester filaments had significantly lower impact resistance than the Polyamides or PLA Pro. All else being equal, the PA612-CF will produce a more durable part than any of the Polyesters. However, ~500 mFTLB is still sufficient for many parts and has not been found to be an issue during real world testing. Hence the Polyesters cannot be dismissed simply due to this metric.
The wide spread in layer adhesion among the polyesters was not expected, and strongly favors the BB PET-CF. The PA612-CF was within about 25% of the BB PET-CF and remains competitive.
It must be noted again here that layer adhesion is highly dependent on how close the old layer temperature is to the melt point of the filament. A higher ambient temperature will drive a higher old layer temperature and increase layer adhesion. The spread between the filament may be different under these hotter conditions. All samples tested here were printed at ~80 F.
Setting PLA Pro aside due to its poor temperature resistance, we are left with two filaments. The BB PET-CF and the PA612-CF. The BB PET-CF has the advantages of no requirement for annealing, less creep, and slightly improved layer adhesion. The PA612 has the advantage of significantly greater impact resistance, and due to being a Nylon, good wear resistance.
If the requirement to anneal the PA612-CF was set aside, it would most likely be the filament of choice. However, annealing is a process that requires compensation for shrinkage and can be complex for larger parts. Because of this the BB PET-CF remains competitive.
The ranking of filaments will be done as follows:
Polymaker PLA Pro is best for those who would like to print mechanical parts easily and at low cost without concern for long term use in elevated temperatures.
Bambu PET-CF is a more costly option for those who wish to make permanent mechanical parts that can resist elevated temperatures.
Polymaker PA612-CF is the best option for long term durable parts printed by advanced users with an understanding of the annealing process.
Appendix
The stress strain curves for all twelve filaments are illustrated here. The horizontal axis is strain and the vertical is stress in PSI. All charts are the same scale to make comparisons easier.
Special comment is owed to the PA6-CF as it slowly popped out of the testers jaws soon after necking began. This is the cause of the rather odd irregular lines after the yield point.
The slope of the line represents the stiffness, the steeper the slope the greater the stiffness. The yield begins as the line begins to curve downwards to a lesser slope.
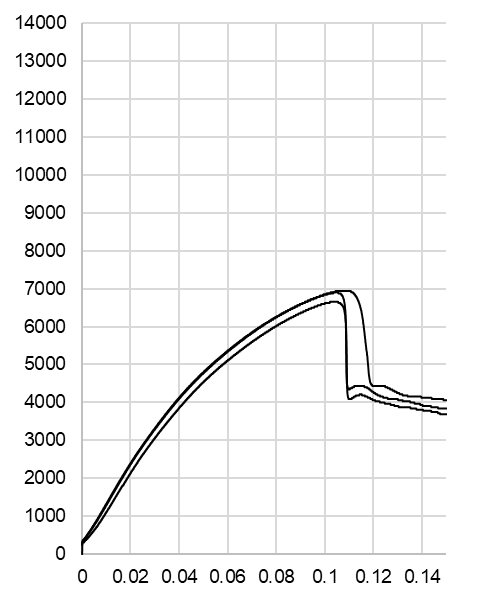
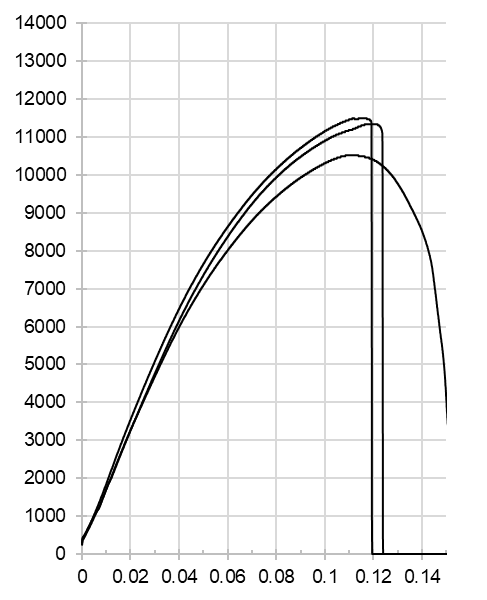
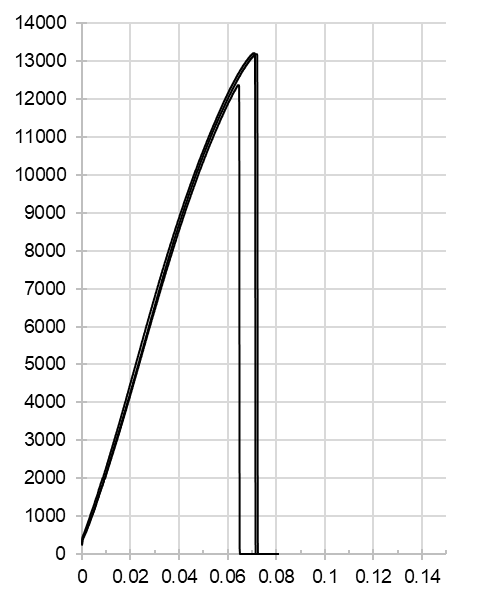
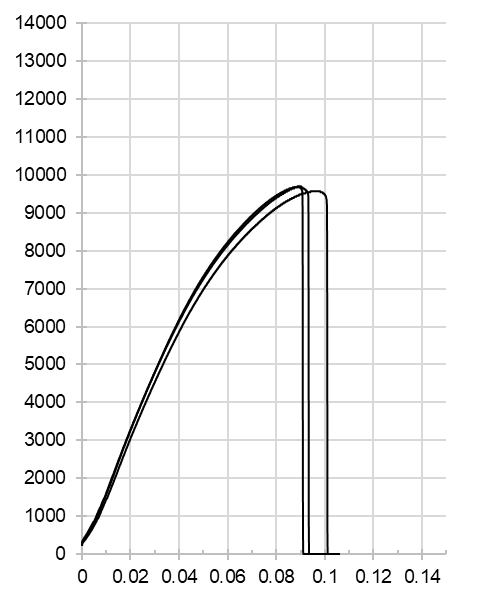
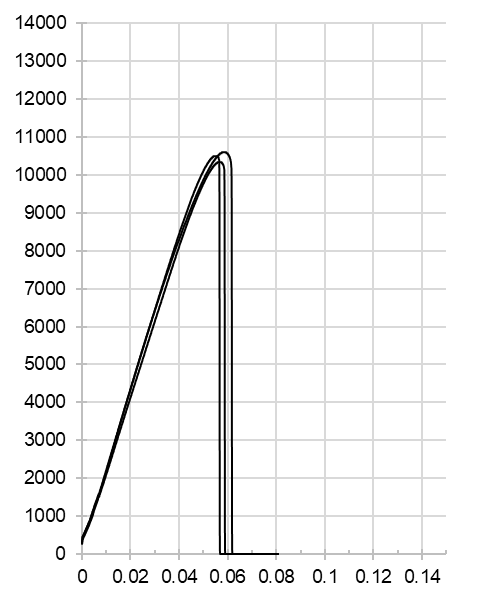
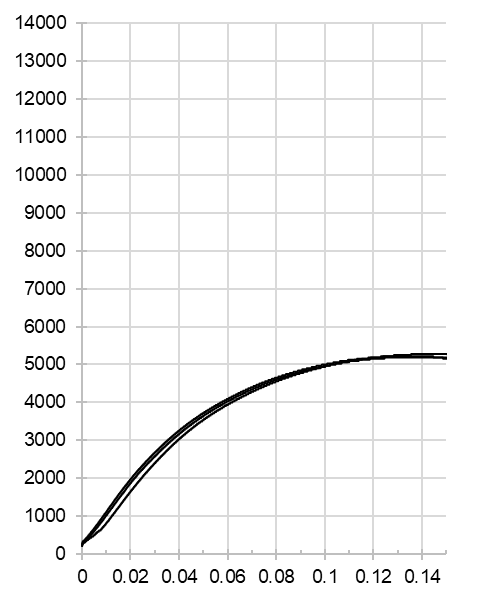
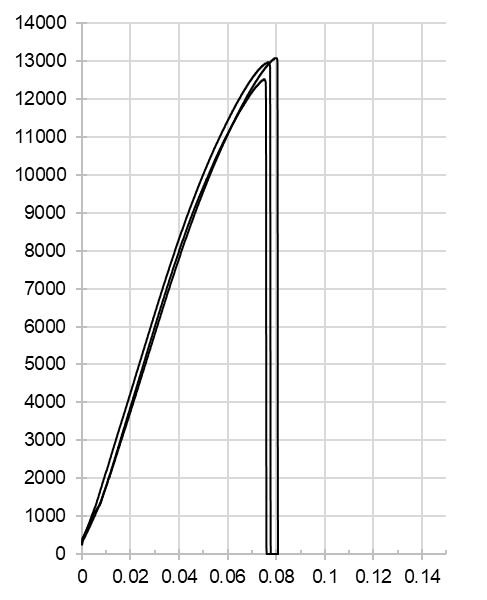
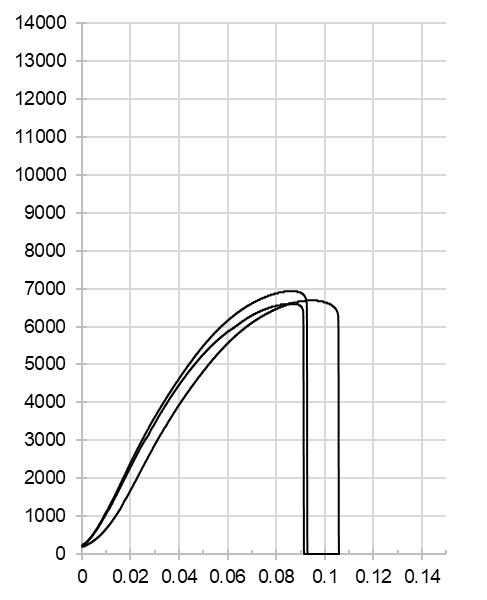
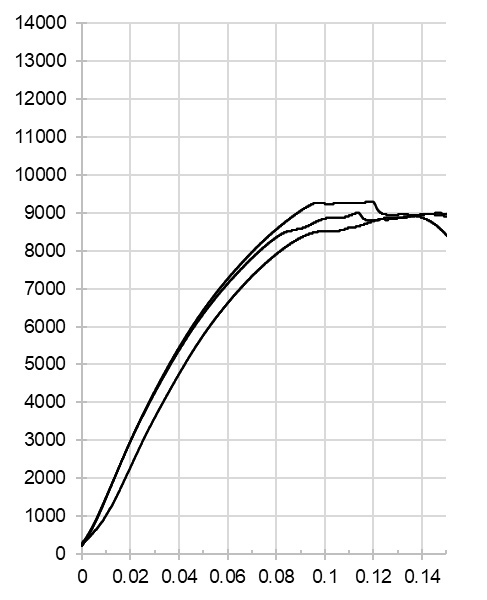
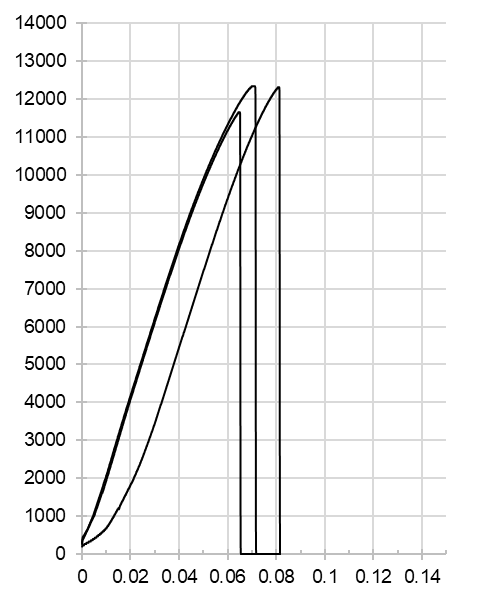
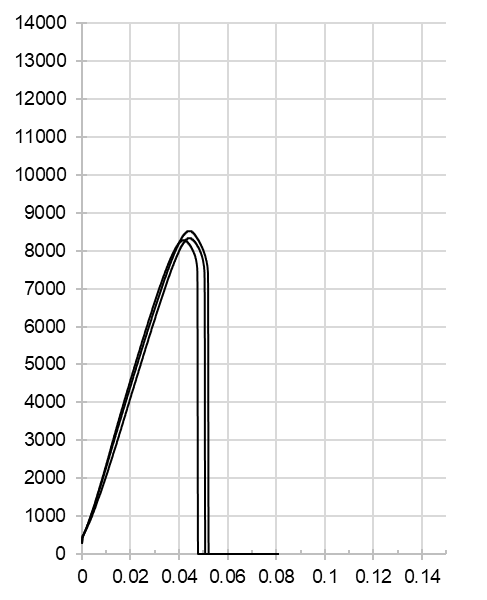
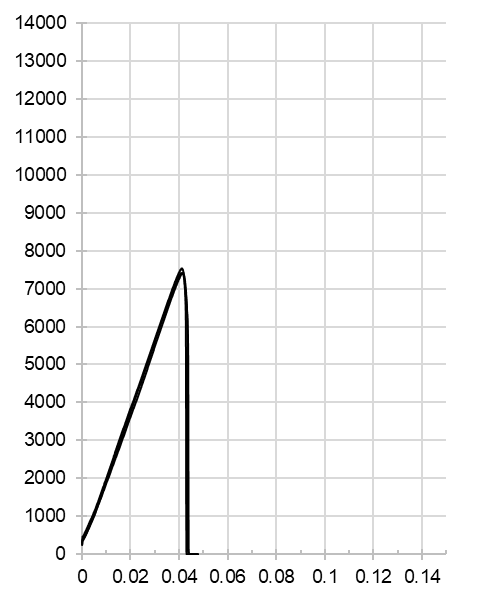