I recently conducted a series of mechanical tests on the Taulman3D Glass Fiber Nylon. The goal was to understand how annealing effected the properties of the Nylon. I also tested how water absorption from the atmosphere effected the mechanical properties, and how soaking in oil and annealing can combat the effects of moisture.
These results should be similar to other Nylons. I am not sure what the exact make up of the Taulman Nylon is, but it appears to be a Nylon 6 blend. I am currently conducting testing with the Polymaker PA12-CF Nylon, and it will be interesting to see how it is effected compared to the Taulman Nylon.
Nylons suffer from a phenomenon called Creep. This is where a part develops strain when loaded for a prolonged period of time at a stress level well below the excepted yield point of the material. In other words, the material slowly flows while under pressure. High fiber content filled Nylons still suffer from this, but not as much as unfilled Nylons. My first test was to determine if annealing fixed this issue.
My process for annealing is to bake the samples at 185 F for two hours, and then allow them to cool slowly to room temperature.
The samples where printed flat on the bed using aligned rectilinear infill. Below can be seen one of the samples during the test, two holes where added to each side of the test zone to allow the samples to be measured before and after the test.
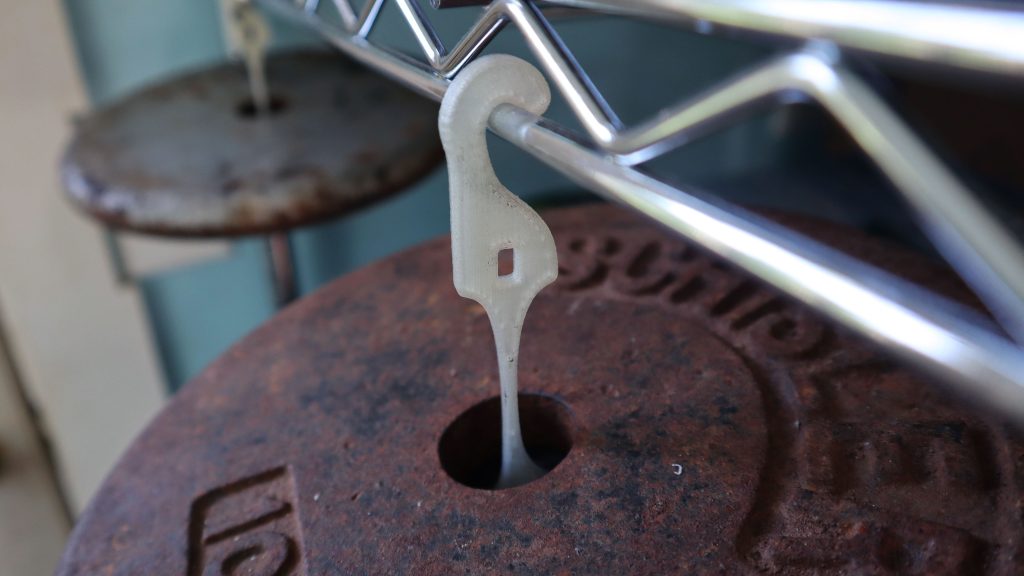
The samples where moisture conditioned for 12 hours at atmospheric humidity levels prior to testing. Samples where then hung with a ten pound weight for 51 hours. This worked out to approximately 100 PSI of constant stress. The strain results can be seen below. It is clear that the annealing greatly reduced the amount of creep.
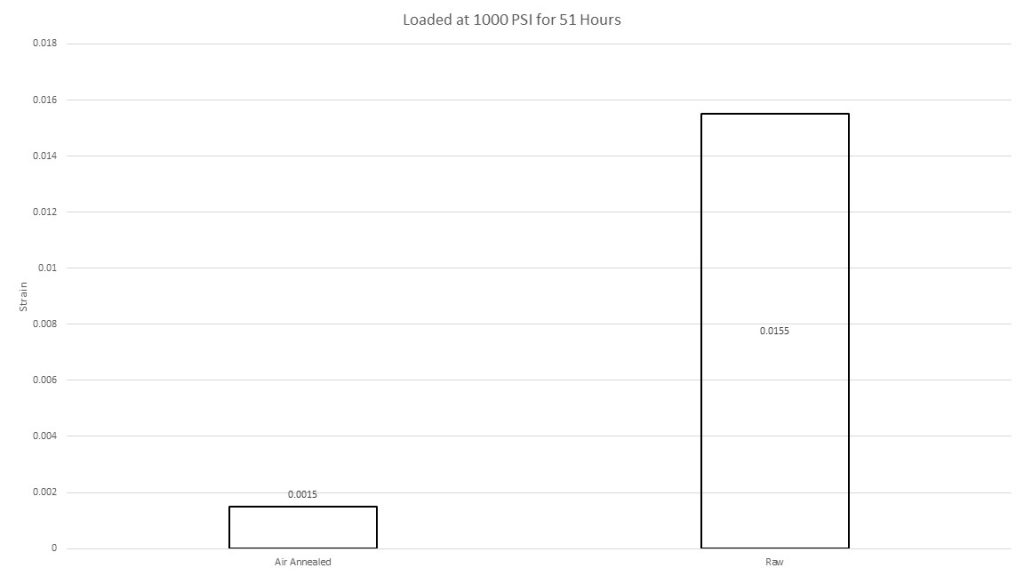
The next test I conducted was to to determine how annealing effected the impact resistance. Two sets of three impact samples where printed. As before, the samples where printed flat with 100% aligned rectilinear infill. This is done to insure that the absolute material properties are tested, and layer adhesion is not a factor. The samples where moisture conditioned for several weeks prior to testing. I unfortunately did not have a control group of dry samples, so I do not know how the moisture effects the impact resistance, though my guess is the dry samples would have a much lower impact resistance.
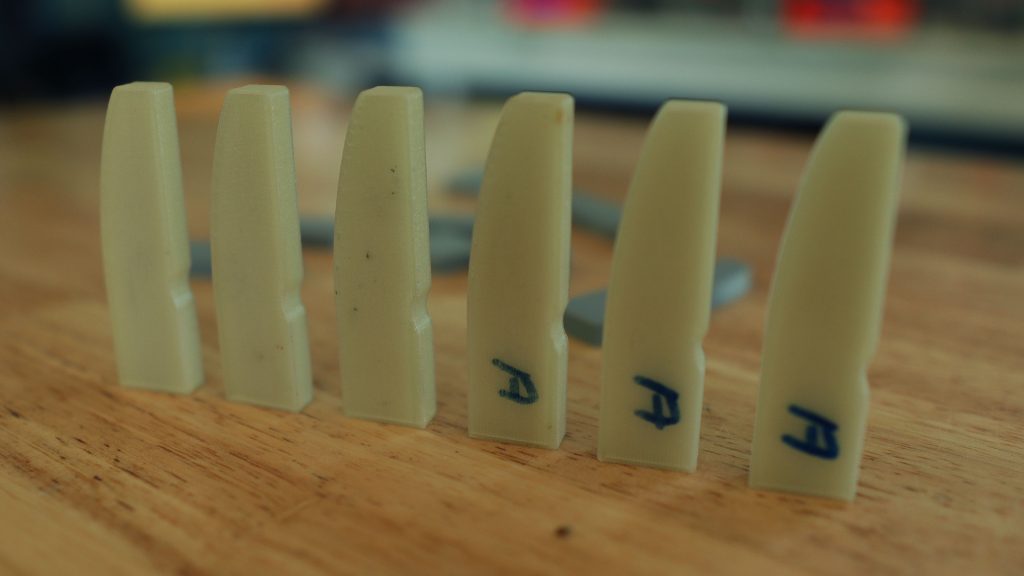
For comparison purposes I also tested the Polymaker PLA Pro, which has good impact properties. The average results of the sample sets can be seen below. Units are in HIU’s, or the amount of energy that the sample absorbed when it was broken by the falling hammer.
It is clear that the annealed samples had a lower impact resistance, but not by much. Both sets of Nylon samples had incredible impact resistance compared with the already respectable PLA Pro.
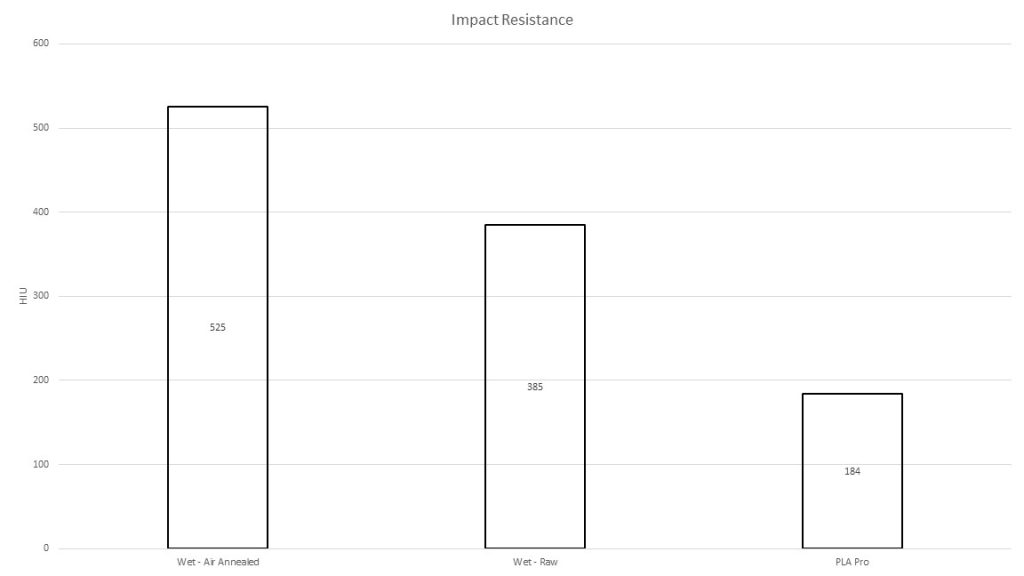
The final test was the most interesting, it is a tensile test. The goal was to understand how annealing and atmospheric moisture effected the strength and stiffness of the Nylon. Below you can see one of the PLA Pro samples being tested.
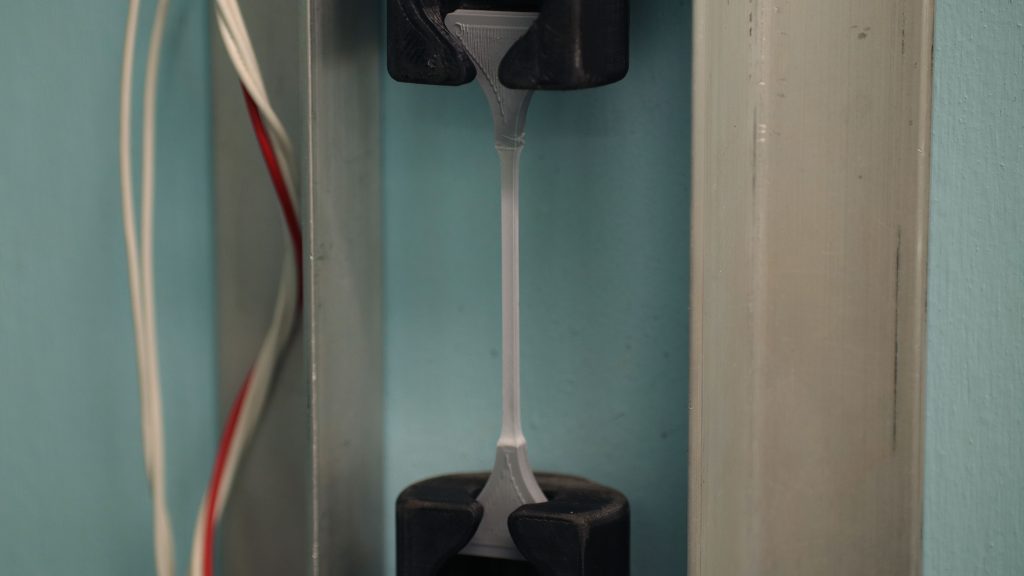
Eighteen Nylon tensile test samples where printed. These where broken up into three groups, one was left unprocessed (Raw), one was annealed in air at 185 F for two hours (Air Annealed), and the third was annealed in an oil bath at the same temperature and time (Oil Annealed). The oil annealed samples was allowed to soak at room temperature in the oil for an additional 24 hours. All samples where stored in a dry box after printing or annealing to prevent water absorption.
The oil used is a 5W light machine oil. The idea behind the oil annealing is that the oil will fill the voids in the Nylon and prevent water absorption.
After the samples where processed, the three groups where each split again. Half of each group was left in the dry box and the other half was left out to absorb moisture for two weeks. Humidity levels where above 50% and temperatures where above 80 F for the majority of the time.
After two weeks all of the samples where tested on my tensile testing machine. The stress strain curves are shown below, once again PLA Pro is used as a reference. Keep in mind that my testing machine does not have a proper strain gauge, strain data is very approximate and should only be used for comparisons within this test. The same goes for Young’s Modulus data.
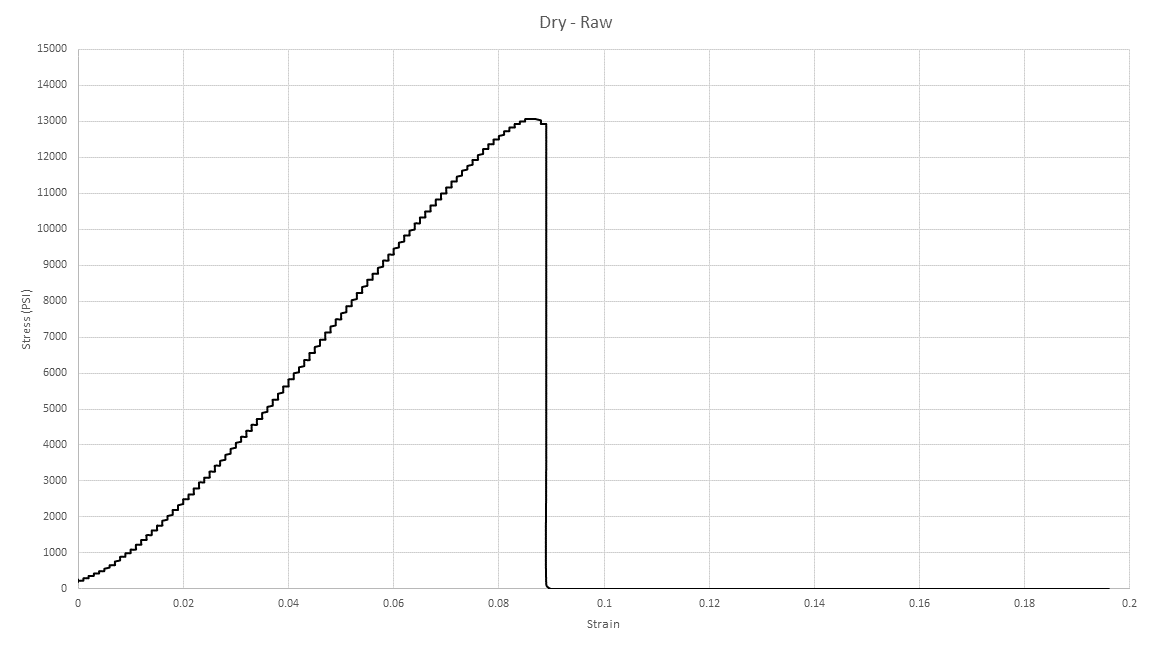
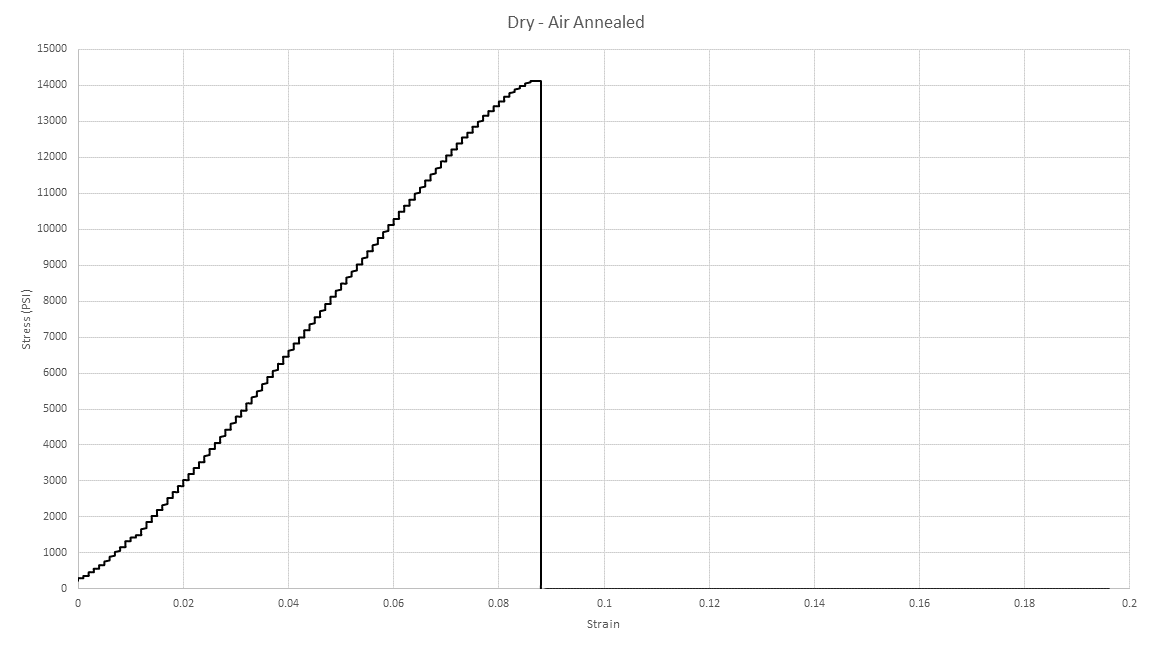
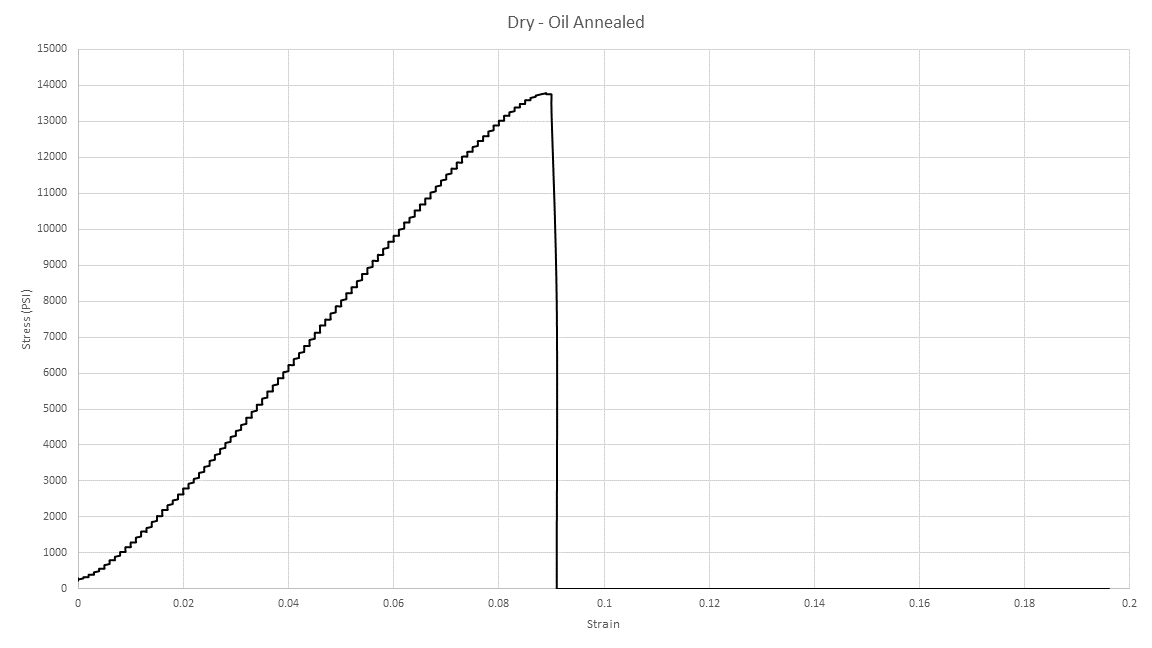
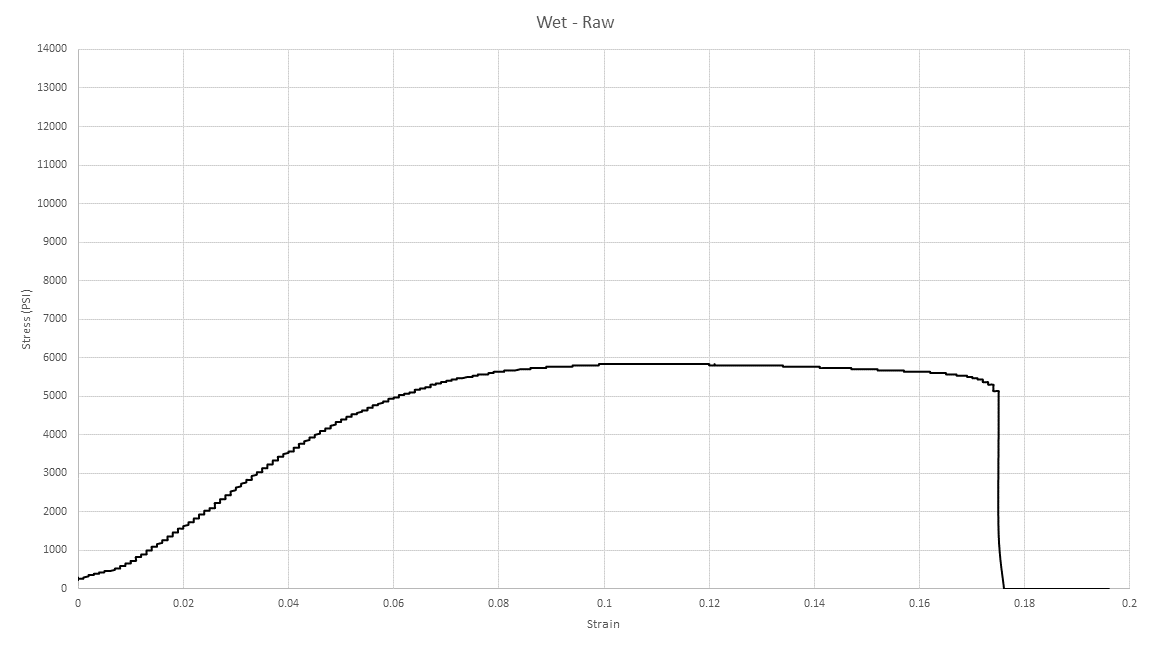
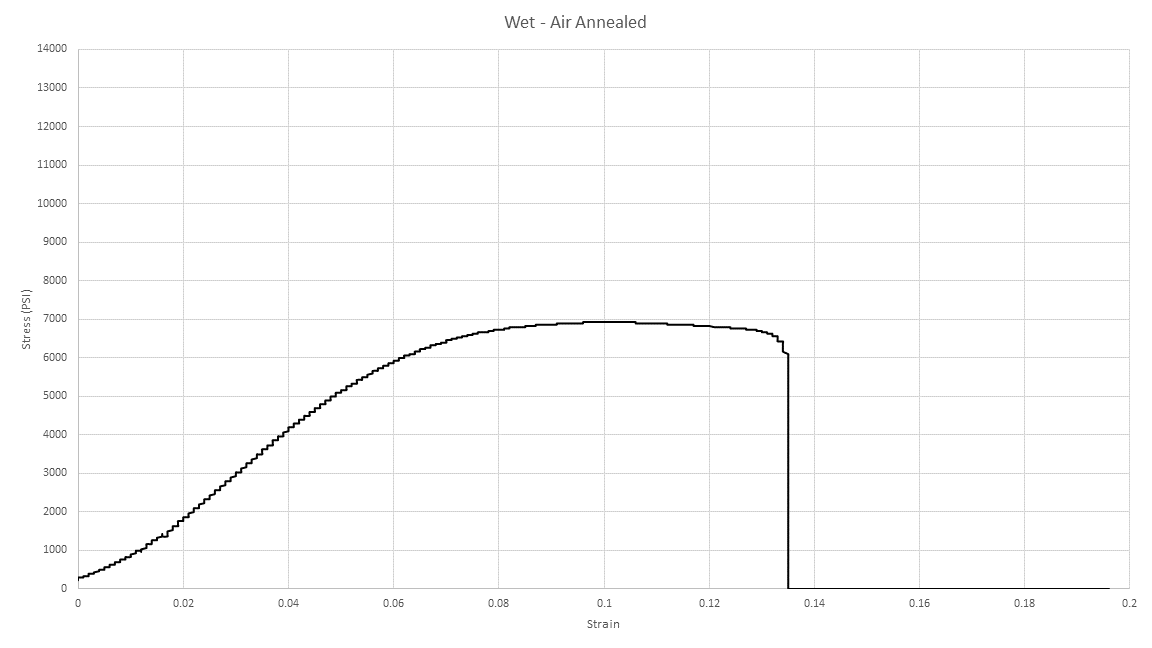
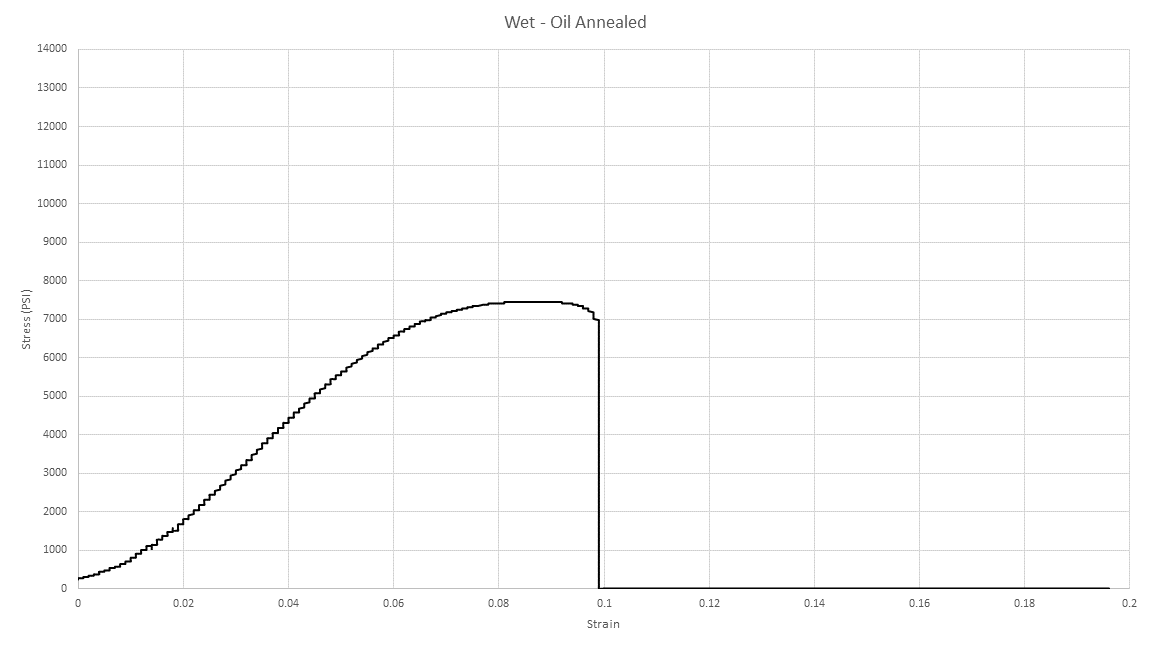
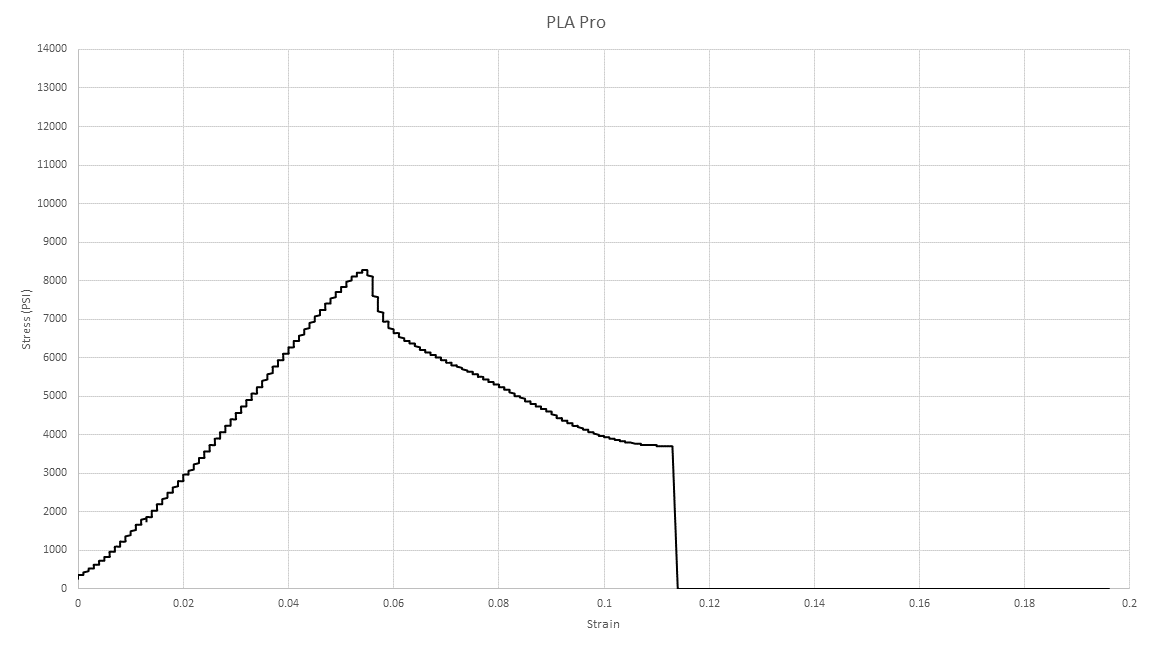
The ultimate tensile strength is shown below. A few things can be learned from this data.
- The dry samples are far stronger then the wet samples.
- Annealing increases the strength of the samples, wet or dry.
- The dry oil annealed samples are stronger then the raw samples, but weaker then then the air annealed samples. This indicates that the oil has a similar effect to water, but to a far lesser degree.
- The wet oil annealed sample was stronger then the wet air annealed sample, this indicates that the oil is indeed inhibiting water absorption, at least to a certain extent.
- All of the wet Nylon samples are weaker then the Polymaker PLA Pro. Making them unsuitable for many parts.
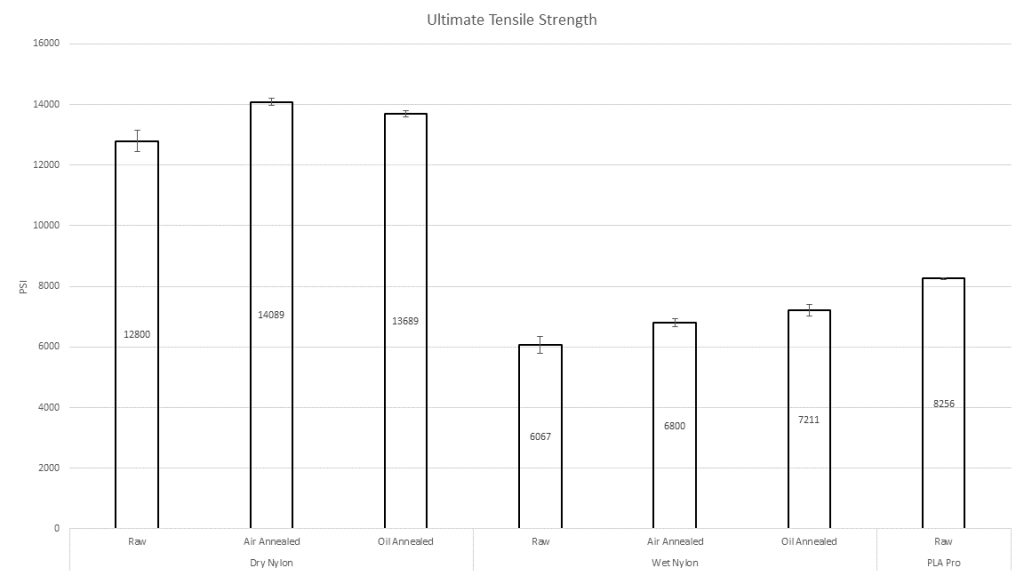
The Young’s Modulus is really a more important metric then ultimate tensile strength. It is basically a measure of the stiffness of the material. Below you can see the results computed from the stress-strain data. The results lead to similar conclusions as before, except the discrepancy between the PLA Pro and wet Nylons is greater.
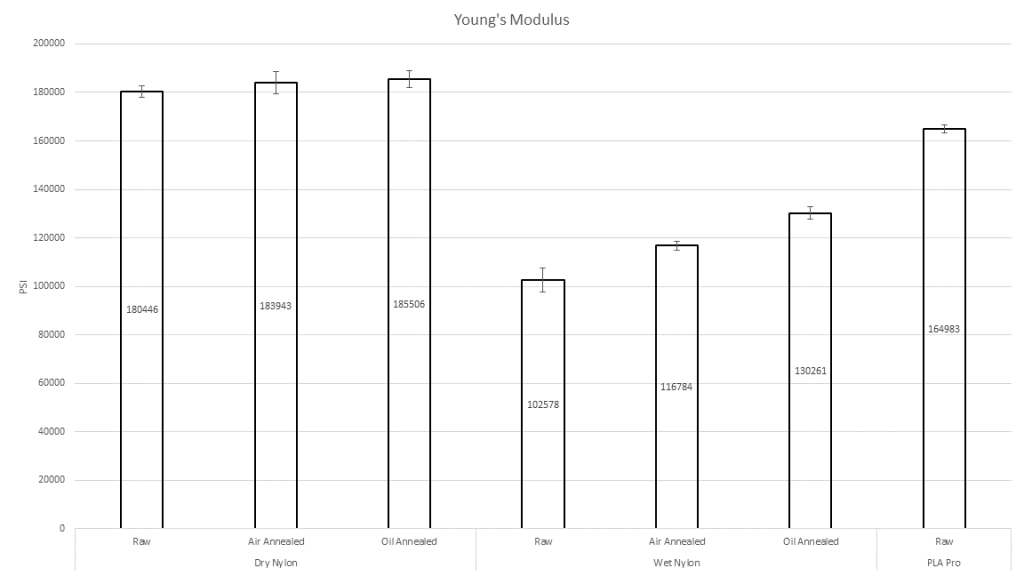
The yield strength is the point where the material transitions from elastic to plastic deformation. It is always a bit lower then the ultimate tensile strength, and in some cases a lot lower. The below graph compares the before shown ultimate strength to the estimated yield strength.
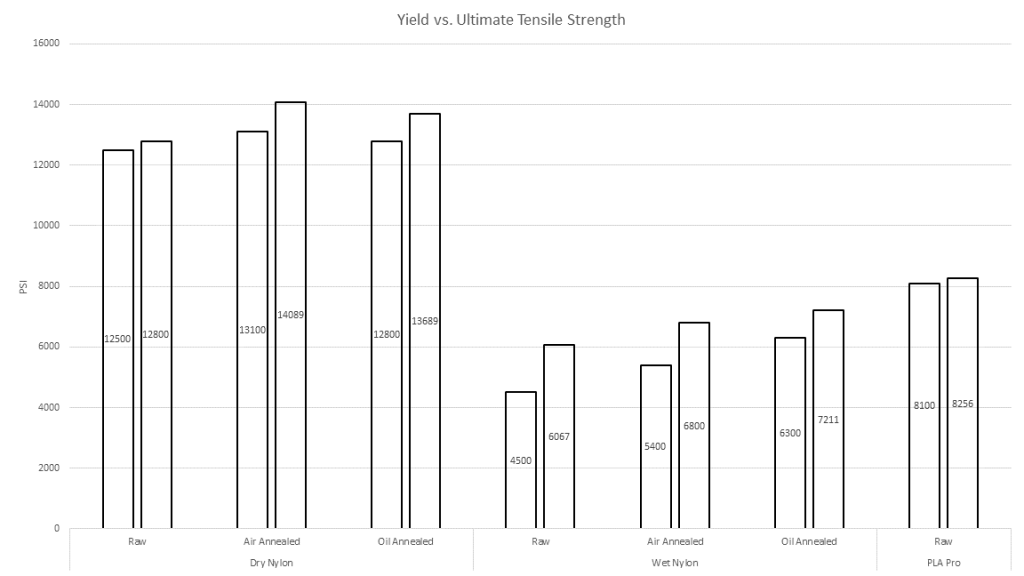
I have presented the data here in a format that should allow you to come to your own conclusions. However, here are the main take always I had.
- Annealing solves the creep issues with Nylon.
- Annealing degrades the impact resistance, but not enough to be significant.
- Annealing improves the stiffness and strength of Nylon, but not enough to offset the effects of moisture.
- Moisture absorbed from the air has a devastating effect on the strength and stiffness of Nylon.
- Oil infused in the Nylon helps reverse the effects of water, I assume by reducing the amount of moisture that the Nylon can absorb.
If the strength and stiffness of the Nylon can be brought up to the level of PLA Pro, the result would be a tough, impact resistant material that has superior heat resistance to PLA+. I will continue the investigation into the oil treatment, and see if there is a way to increase it’s effect by pressurizing the oil or increasing the duration of the soak.
I am also will be conducting similar tests with the Polymaker PA-12 CF Nylon, and the results will be very interesting. PA12 is less hydroscopic then PA6, and that may make it a better material.
I hope you found this information interesting!
Thanks for taking the time to do these tests, it’s great to read through!
Damn good work. The analysis has clear results for the circumstances. Dumb question, but Nylon 6 isn’t the same as Nylon 66?
I’m actually not sure on that one. Nylon types are complicated!
Thank you for doing this research
So in a nutshell, the Glass Fiber Nylon would be a good filament to print lowers/frames with as long as it’s annealed?
No, even with annealing it is really too flexible.
Love the passion and research. What a crazy time to live in!
Something I am wondering when it comes to Nylon and carbon fiber, is does the original source material the carbon fiber is from effect how well it works with in the polymer of choice, (asbury has nylon polymer made carbon fibers so just kinda wonder if the shape of that carbon backbone is better than others or less effective at working with the nylon like filaments that use it inside it, since often I found it makes the polymer more brittle and not as good at stress handling.